Mexican Public Healthcare Sector
The Instituto Mexicano del Seguro Social, commonly known as IMSS, stands as the largest hospital network in the country. With a history spanning over 80 years, it has consistently catered to the healthcare needs of a significant portion of the population across various levels of care.
Nestled in Monterrey, UMAE 34 represents one of the high-specialty hospitals within the IMSS network. Focused on cardiology, the hospital identified the necessity for a robust blood bank to support its operations.
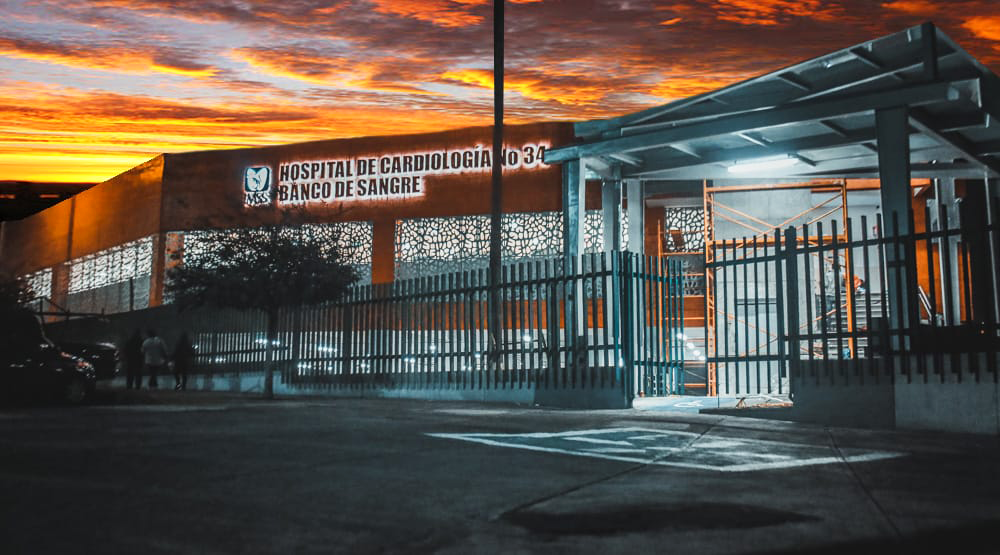
UMAE 34 ‘s blood bank is part of a select group comprising three other banks across the country, serving the major urban centers of Monterrey, Guadalajara, and CDMX. These Central Blood Banks not only supply hematocomponents to their affiliated hospitals but also extend their services to other facilities within the network, spanning different states.
Drawing from my experiences visiting three out of four Central Blood Banks, Monterrey boasts the most advanced infrastructure. Consequently, upgrading their serology department emerged as a critical need.
UMAE 34 Serology Department
With a long-standing reliance on the Abbott Architect platform, transitioning to the latest platform, Alinity, was a natural progression for the serology department.
The department comprised two sub-departments: Donors and Patients. The Donors section housed one Architect i4000 and a backup i2000, while the Patients area featured two i2000 analyzers, with one serving as a backup. This configuration, totaling five processing modules, adequately met the existing demand.
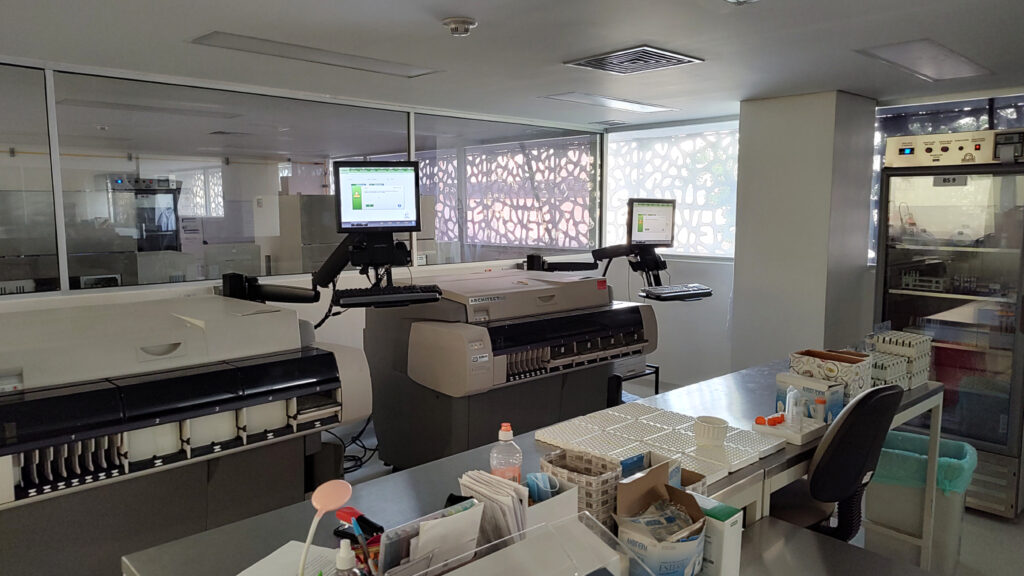
However, changes in local regulations mandated patient serology testing to be centralized in lab centers. Consequently, the previously distinct serology sub-departments needed to be consolidated into a single unit. The adoption of the Alinity S platform aligned with these regulations, as it exclusively focuses on donor testing, unlike the versatile Alinity i.
Training
Prior to executing the upgrade, it was imperative for me to undergo comprehensive Alinity S training to ensure seamless equipment integration. Following a rigorous three-week training program in Dallas, I returned to Monterrey to conduct pre-site inspections, determining optimal equipment placement and installation routes.
Pre-site Inspections and Route Planning
Initially, accessing the main entrance or utilizing the personnel elevator seemed viable options. However, upon closer examination, logistical challenges emerged. Maneuvering the equipment via crane through a low-ceilinged area with an inset access door posed significant risks, and blood collection operations had to be stopped to ingress the instruments [purple path]. Similarly, accessing the elevator proved unfeasible due to spatial constraints, even with attempts at maneuvering the equipment [blue path].
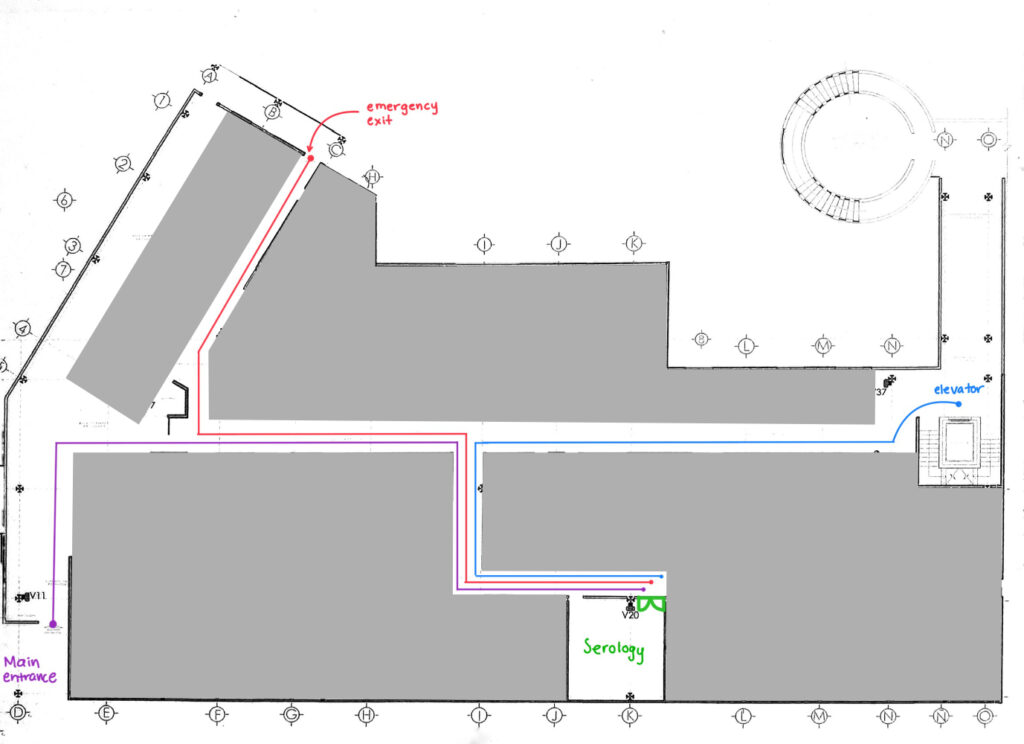
A breakthrough occurred during a moment of reflection. While pondering potential solutions, I noticed the emergency exits and speculated whether they could accommodate the equipment. Subsequent measurements revealed a minor discrepancy in width. Upon discussing this finding with the blood bank supervisor, we weighed the option of modifying the wall to create a wider access path, ultimately receiving approval from the infrastructure department. Additionally, opting for a forklift over a crane was deemed the better choice. From the Blood Bank operation standpoint accessing through the emergency exit did not halt blood collection [red path].
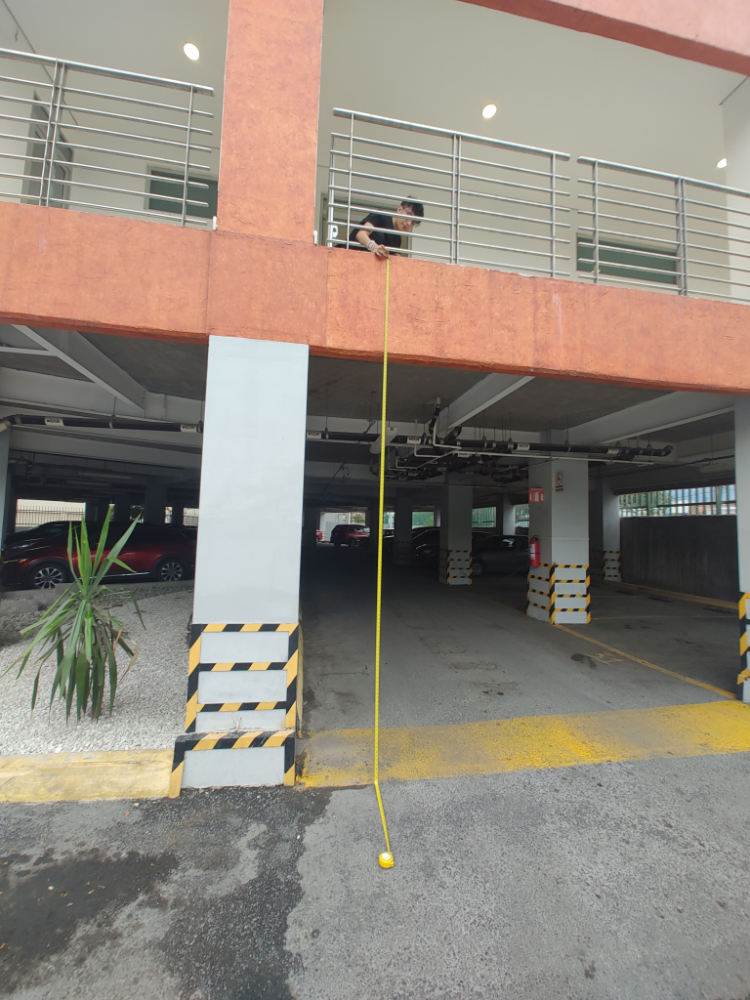
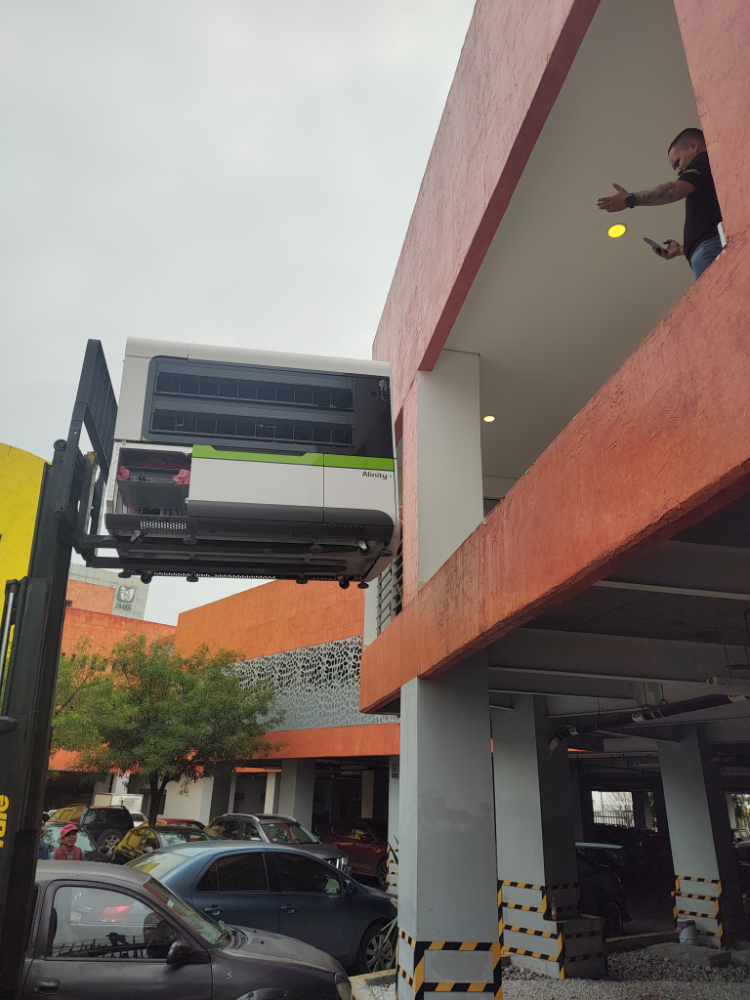
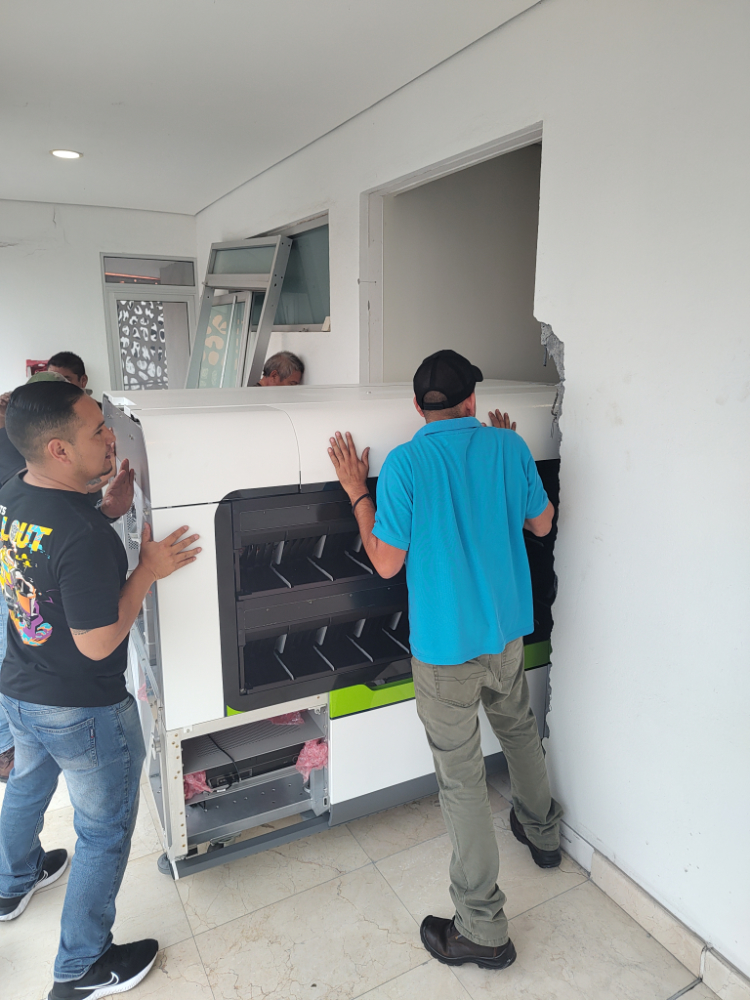
New Layout Design
The chosen location for the new equipment was the former patients’ testing area. Initially, it seemed logical to retain the existing layout, placing the two Alinity S analyzers in the same position as the previous Architects. However, the larger footprint of the Alinity S necessitated reevaluation.
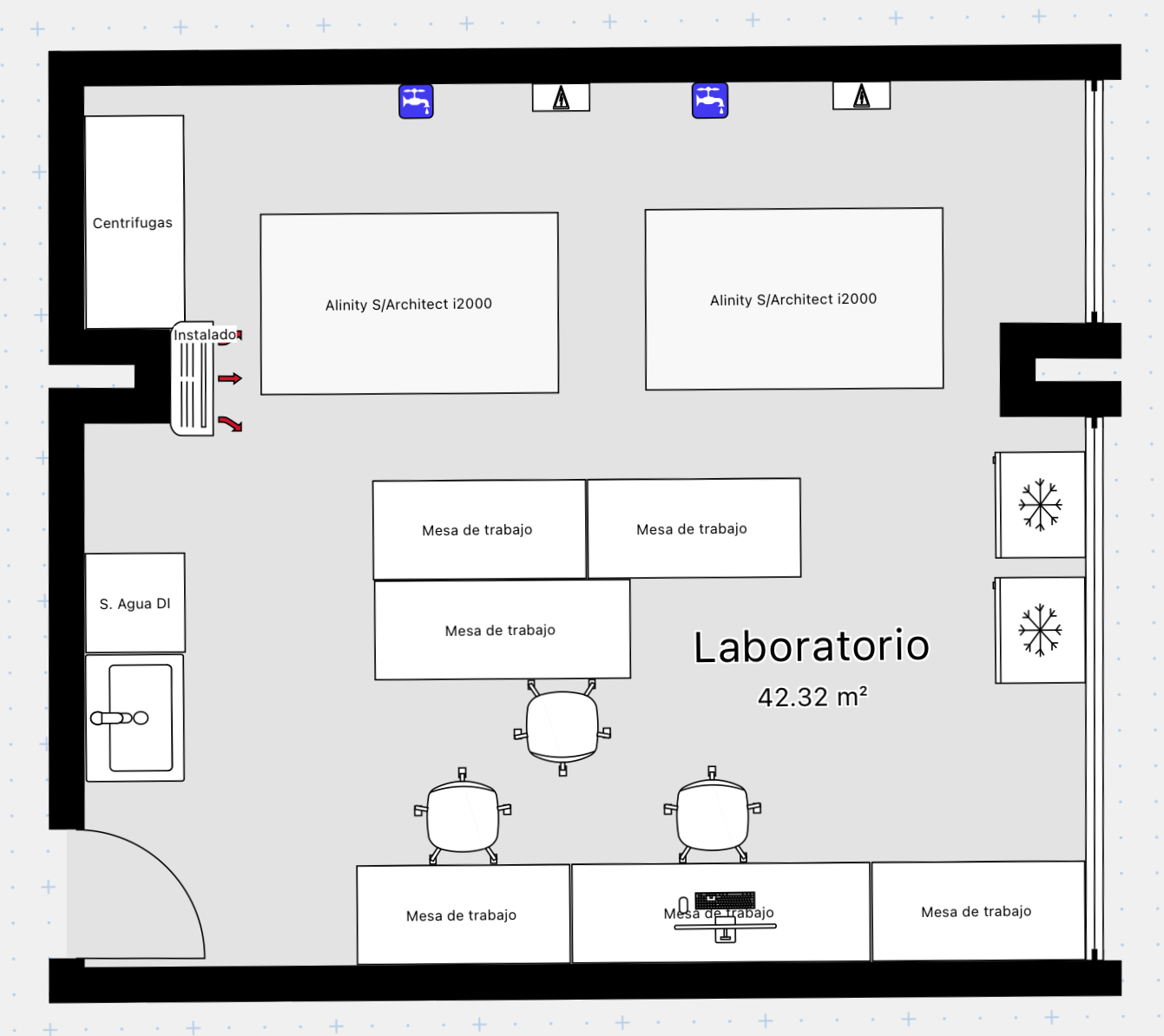
After sketching alternative layouts and consulting with my supervisor and Abbott Latam Transfusion Expert, we settled on rotating the area by 180°. This decision was driven by the presence of protruding columns along the original layout’s east and west walls, hindering clearance space required by the Alinity S.
Upon completion, the equipment faced the north wall, with the east window positioned to its left. This orientation ensured optimal placement of the optic reader, minimizing sun exposure.
Nevertheless, this adjustment was not without its challenges. The existing access door proved inadequate in width for the Alinity S, prompting further modifications. Observations of user interaction patterns revealed a tendency to overlook certain equipment. Consequently, I proposed installing new doors in the vicinity of the overlooked centrifuges, facilitating smoother access.
Creating a 1:1 scale model was instrumental in ensuring the accuracy and feasibility of the proposed modifications. Using black tape to outline the dimensions of the new doors on the floor provided a tangible representation of the intended changes within the physical space. This allowed for a visual assessment of potential obstructions or spatial constraints that might impact the installation process. Additionally, crafting a full-size perimeter of the Alinity S analyzer on paper enabled a meticulous evaluation of its dimensions, considering factors such as packaging, covers, and essential components. By meticulously measuring and testing the equipment’s maneuverability within the confined space, I gained confidence in the accuracy of the proposed modifications. This proactive approach not only facilitated precise planning but also minimized the risk of potential setbacks during the installation phase, ensuring a seamless transition to the new layout design.
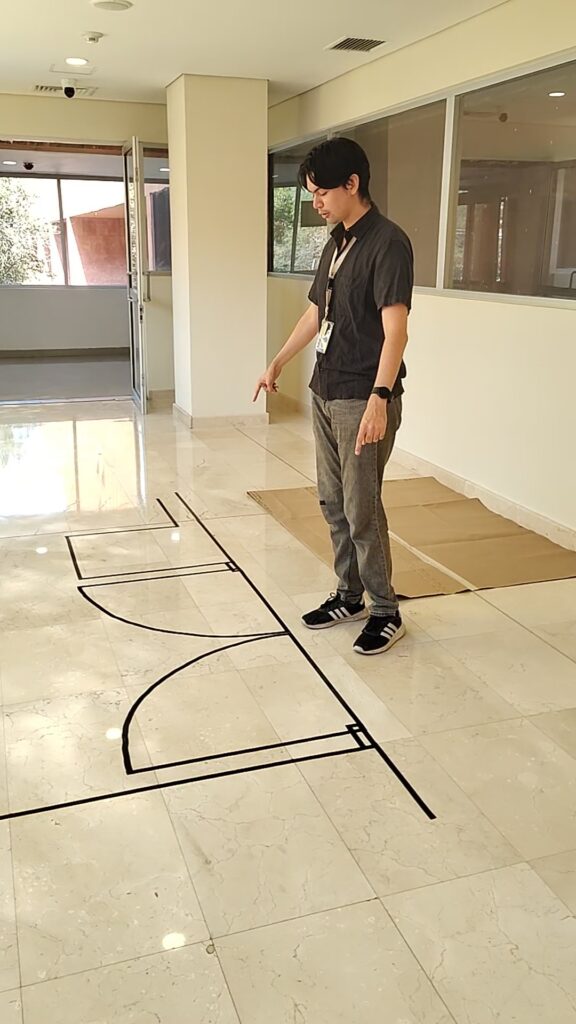
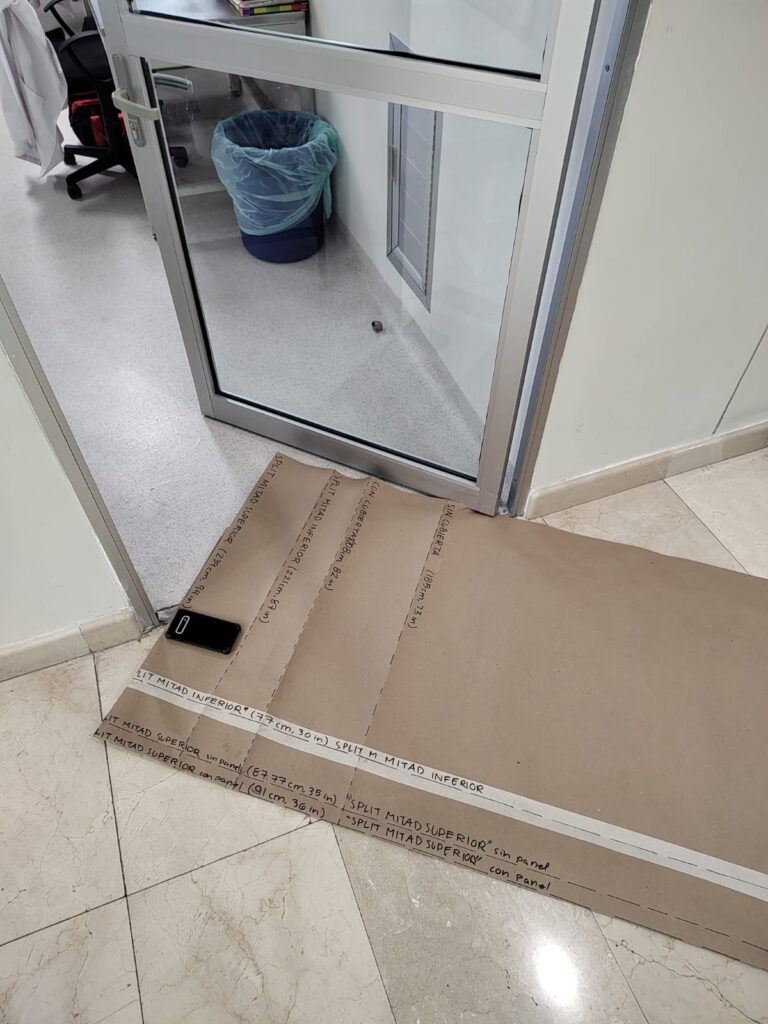
Additional details in the final layout were carefully considered.
- The sink is strategically located near the entrance to facilitate handwashing for personnel entering or exiting the area.
- The computer is positioned at the east window, ensuring that users face the outside, thereby reducing eye fatigue from prolonged monitor use.
- Centrifuges and refrigerators are situated on the opposite side of the room to minimize vibrations and electrical noise that could potentially interfere with sensitive instruments.
- Worktables are oriented to face the instruments, allowing users to easily monitor alerts and notifications.
- Worktables are deliberately offset to one side to prevent users from circumventing the desk while holding samples/reagents, thus reducing the risk of accidental spills or drops.
- The area is divided into three distinct sections: reception at the top, sorting in the middle, and testing at the bottom.
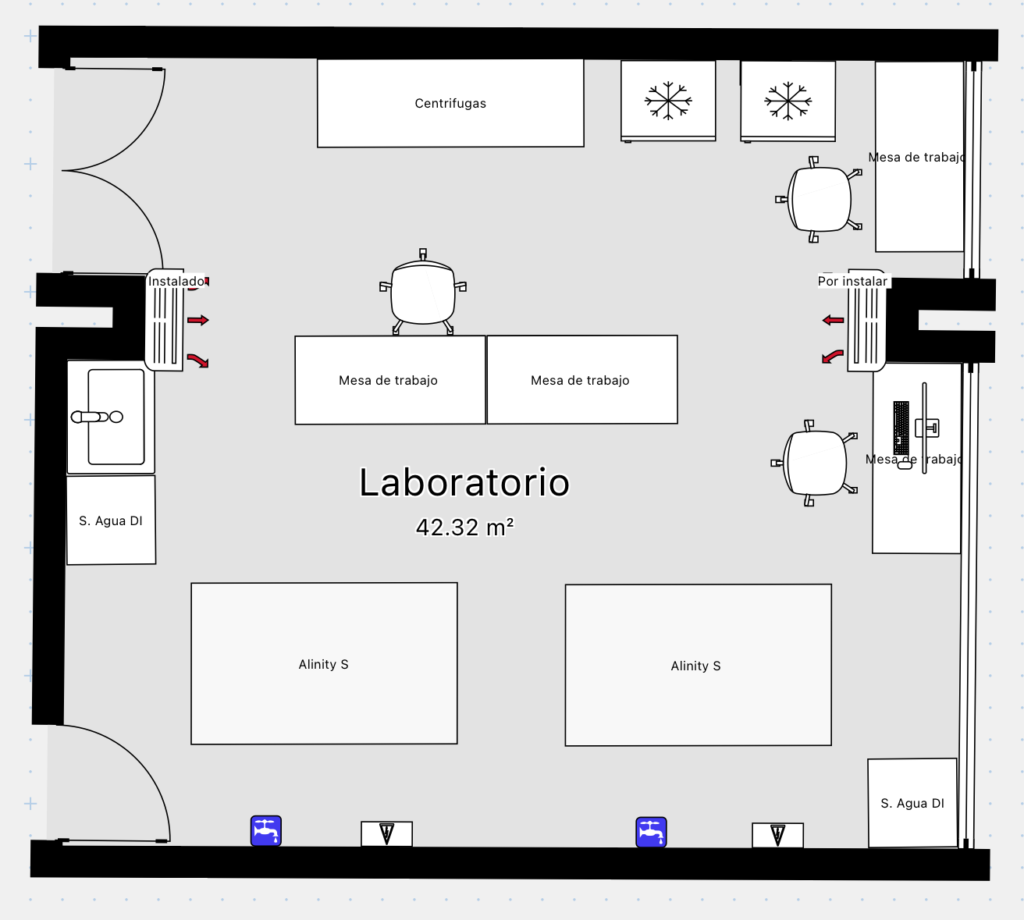
Installation
Despite the thorough planning undertaken, we faced setbacks during the installation process, mainly concerning the scheduling of electricians and coordinating with the DI water provider to establish their corresponding systems. Nonetheless, the first instrument became operational within four days, marking a significant reduction in the average installation time, which typically spans a week.
It’s important to highlight that during the installation process, the integration of two Alinity S analyzers provides functionality equivalent to eight processing modules of the Architect platform. This upgrade not only addresses the current demand but also prepares UMAE 34 for future needs, especially considering the continuous growth of the city of Monterrey.
Conclusion
In conclusion, the successful upgrade of the UMAE 34 serology department exemplifies the importance of thorough planning, innovative problem-solving, and effective collaboration. By addressing logistical challenges and implementing strategic design modifications, we ensured a seamless transition to the new equipment, ultimately enhancing the efficiency and functionality of the blood bank. This project underscores the value of proactive planning and adaptability in achieving project objectives within the healthcare sector.
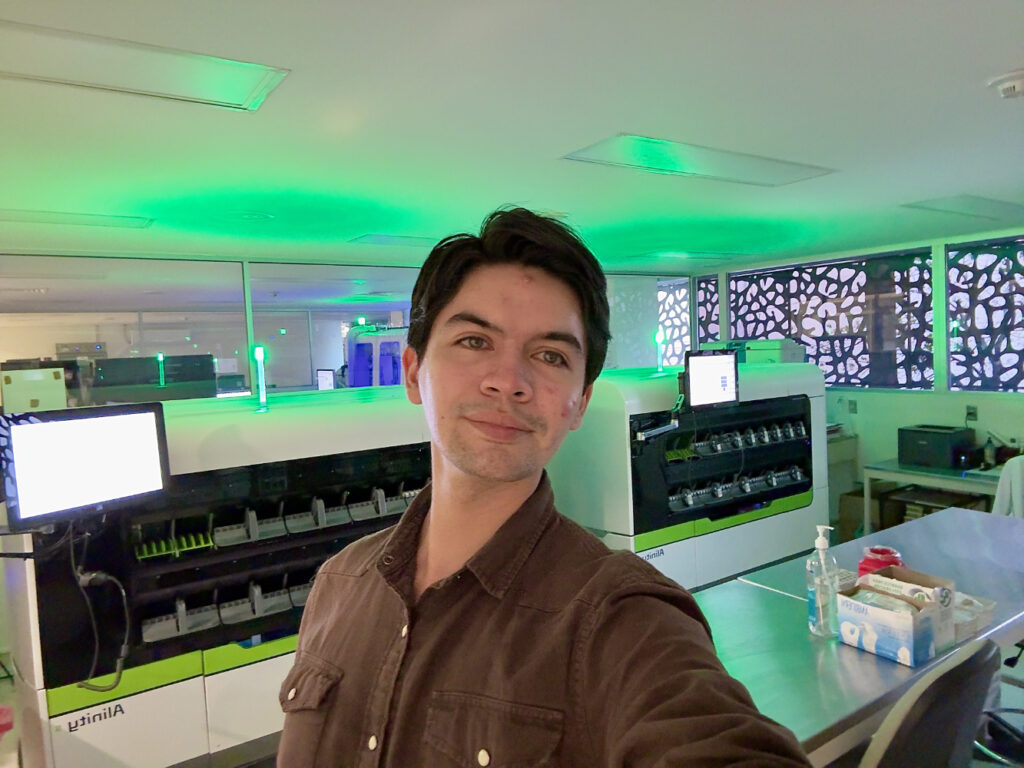